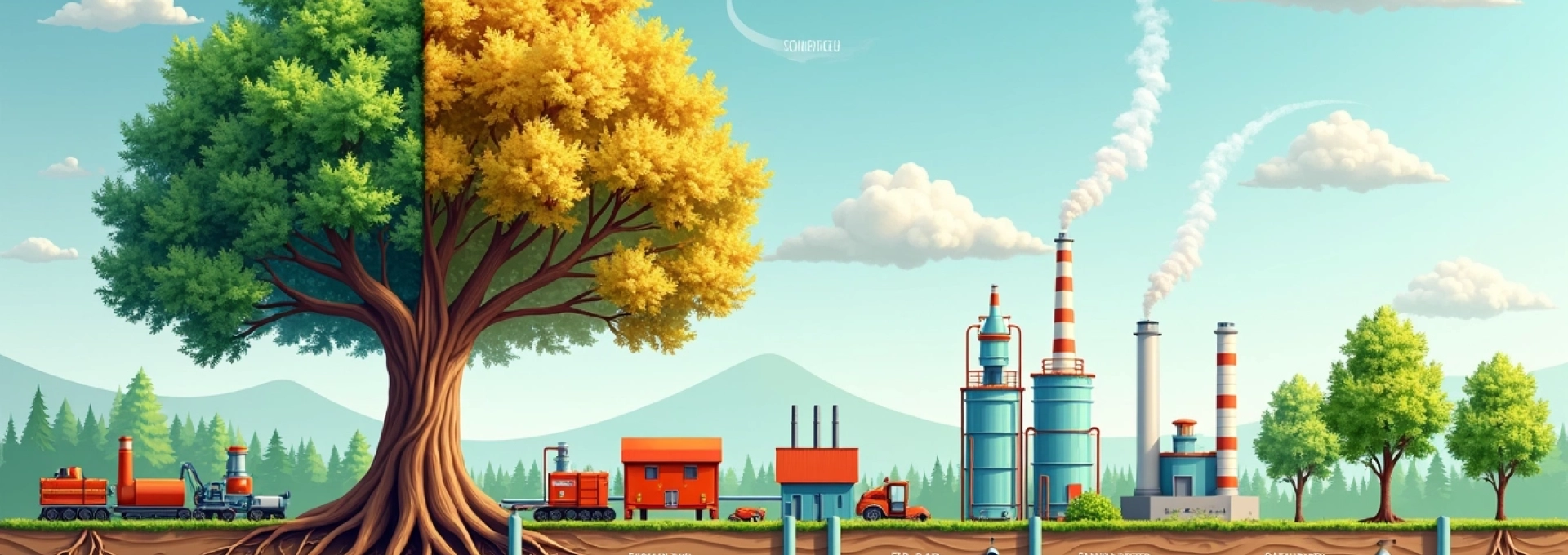
Les plaquettes forestières représentent une solution énergétique renouvelable en plein essor. Issues de la valorisation des résidus d'exploitation forestière, elles offrent une alternative écologique aux combustibles fossiles. Leur utilisation croissante dans les chaufferies collectives et industrielles témoigne de leur potentiel pour la transition énergétique. Mais que sont exactement ces plaquettes et comment sont-elles produites ? Quelles sont leurs caractéristiques et leurs applications ? Découvrons ensemble les enjeux techniques, économiques et environnementaux de cette filière prometteuse.
Composition et caractéristiques des plaquettes forestières
Les plaquettes forestières sont des petits morceaux de bois obtenus par déchiquetage de résidus forestiers. Leur composition varie selon la ressource utilisée, mais on distingue généralement trois grandes catégories :
- Les plaquettes vertes, issues directement de l'exploitation forestière
- Les plaquettes sèches, obtenues après séchage naturel ou artificiel
- Les plaquettes de scierie, provenant des chutes et résidus de sciage
La granulométrie des plaquettes est un critère essentiel qui détermine leur utilisation. On trouve principalement des calibres allant de 5 à 50 mm, avec une teneur en fines (particules inférieures à 3,15 mm) variable. L'humidité est également un paramètre clé, influençant directement le pouvoir calorifique du combustible. Les plaquettes vertes présentent généralement une humidité de 40 à 50%, tandis que les plaquettes sèches se situent entre 20 et 30%.
Le pouvoir calorifique inférieur (PCI) des plaquettes varie ainsi de 2 à 4 MWh/tonne selon leur humidité. À titre de comparaison, le PCI du fioul domestique est d'environ 10 MWh/tonne. Cette différence s'explique par la densité énergétique plus faible du bois, compensée par son caractère renouvelable et son bilan carbone neutre.
La composition chimique des plaquettes forestières dépend de l'essence de bois utilisée. On y retrouve principalement de la cellulose, de l'hémicellulose et de la lignine, ainsi que des éléments minéraux en faible quantité. Cette composition influence la combustion et la production de cendres.
Procédés de production et matériel spécialisé
La production de plaquettes forestières fait appel à des équipements spécifiques, adaptés aux différentes étapes du processus. De l'abattage au conditionnement final, chaque phase requiert un matériel performant et adapté aux contraintes du terrain.
Déchiqueteuses à tambour pour bois rond
Les déchiqueteuses à tambour sont les machines les plus couramment utilisées pour la production de plaquettes à partir de bois rond. Elles se composent d'un tambour rotatif équipé de couteaux qui déchiquettent le bois en passant à travers une grille calibrée. Ces machines peuvent traiter des diamètres allant jusqu'à 60 cm et offrent des débits importants, de l'ordre de 100 m³/h pour les plus puissantes.
Le choix de la déchiqueteuse dépend de plusieurs facteurs :
- Le type de ressource à traiter (bois rond, branches, souches)
- Le volume de production visé
- La granulométrie souhaitée
- Les contraintes de mobilité (machines fixes ou sur châssis routier)
Les déchiqueteuses modernes intègrent souvent des systèmes d'alimentation automatisés et des dispositifs de régulation de la granulométrie, permettant d'optimiser la qualité des plaquettes produites.
Broyeurs à marteaux pour branches et résidus
Pour les branches et résidus de plus petit diamètre, les broyeurs à marteaux constituent une alternative intéressante. Ces machines utilisent des marteaux mobiles fixés sur un rotor pour broyer le bois contre une enclume ou une grille. Elles offrent une grande polyvalence et peuvent traiter des matériaux hétérogènes, y compris des résidus verts.
Les broyeurs à marteaux présentent l'avantage de produire des plaquettes plus homogènes, avec moins de longues particules que les déchiqueteuses à tambour. Cependant, leur débit est généralement plus faible et ils sont moins adaptés au traitement de gros diamètres.
Cribles vibrants et trommel pour calibrage
Après le broyage ou le déchiquetage, les plaquettes peuvent nécessiter un calibrage pour répondre aux exigences des utilisateurs finaux. Deux types d'équipements sont couramment utilisés à cet effet :
Les cribles vibrants utilisent des grilles oscillantes pour séparer les particules selon leur taille. Ils permettent d'éliminer les fines et les surdimensionnés, assurant une granulométrie homogène. Leur efficacité dépend de la vitesse et de l'amplitude des vibrations, ainsi que de l'inclinaison des grilles.
Les trommels, ou cribles rotatifs, sont des cylindres perforés tournant autour d'un axe légèrement incliné. Les plaquettes y progressent par gravité, les particules fines passant à travers les perforations tandis que les éléments plus gros sont évacués en bout de tambour. Ces équipements offrent une bonne capacité de traitement et s'avèrent particulièrement efficaces pour les plaquettes humides.
Séchoirs rotatifs et à bande pour contrôle d'humidité
Le séchage des plaquettes permet d'augmenter leur pouvoir calorifique et d'améliorer leurs conditions de stockage et de combustion. Deux technologies principales sont utilisées :
Les séchoirs rotatifs consistent en un tambour tournant dans lequel les plaquettes sont exposées à un flux d'air chaud. Ce type de séchoir offre une grande capacité de traitement et une bonne homogénéité du séchage. Il nécessite cependant un apport d'énergie important et peut générer des émissions de poussières.
Les séchoirs à bande transportent les plaquettes sur un tapis perforé traversé par un flux d'air chaud. Cette technique permet un meilleur contrôle de la température et du temps de séjour, limitant les risques de dégradation du bois. Elle est particulièrement adaptée aux plaquettes destinées à des usages exigeants, comme la gazéification.
Le choix de la méthode de séchage dépend de facteurs tels que le volume à traiter, l'humidité initiale et finale visée, et la disponibilité d'une source de chaleur (par exemple, la récupération de chaleur fatale d'une installation industrielle).
Normes et classifications des plaquettes forestières
Pour garantir la qualité et la performance des plaquettes forestières, des normes et systèmes de classification ont été mis en place. Ces référentiels permettent de standardiser les caractéristiques du combustible et de faciliter les échanges commerciaux.
Norme ISO 17225-4 pour biocombustibles solides
La norme ISO 17225-4
est la référence internationale pour la classification des plaquettes de bois à usage énergétique. Elle définit les spécifications et les classes de qualité pour les plaquettes destinées à un usage non industriel. Cette norme prend en compte plusieurs paramètres :
- L'origine et la source de la biomasse
- La granulométrie
- La teneur en humidité
- La teneur en cendres
- La densité apparente
L'adoption de cette norme permet d'assurer une meilleure traçabilité et une qualité constante du combustible, facilitant ainsi son utilisation dans les chaufferies automatisées.
Classes granulométriques P16S, P31S, P45S
La granulométrie des plaquettes est un critère essentiel pour leur utilisation dans les chaudières. La norme ISO 17225-4 définit plusieurs classes granulométriques, dont les principales sont :
Classe | Dimension principale | Fraction fine max | Fraction grossière max |
---|---|---|---|
P16S | 3,15 mm ≤ P ≤ 16 mm | ≤ 15% < 3,15 mm | ≤ 6% > 31,5 mm |
P31S | 3,15 mm ≤ P ≤ 31,5 mm | ≤ 10% < 3,15 mm | ≤ 6% > 45 mm |
P45S | 3,15 mm ≤ P ≤ 45 mm | ≤ 10% < 3,15 mm | ≤ 10% > 63 mm |
Ces classes permettent d'adapter la granulométrie des plaquettes aux spécifications techniques des chaudières, optimisant ainsi leur fonctionnement et leur rendement.
Taux d'humidité M10 à M55+
L'humidité des plaquettes joue un rôle crucial dans leur pouvoir calorifique et leur comportement en combustion. La norme ISO 17225-4 définit plusieurs classes d'humidité, allant de M10 (≤ 10% d'humidité) à M55+ (> 55% d'humidité). Les classes les plus couramment utilisées sont :
- M20 : ≤ 20% d'humidité, idéal pour les petites chaudières
- M30 : ≤ 30% d'humidité, adapté aux chaudières de moyenne puissance
- M40 : ≤ 40% d'humidité, pour les grosses chaufferies industrielles
Le choix de la classe d'humidité dépend des capacités de la chaudière et des conditions de stockage disponibles. Une humidité trop élevée peut entraîner des problèmes de combustion et réduire l'efficacité énergétique du système.
Teneur en cendres A0.5 à A10+
La teneur en cendres des plaquettes forestières est un indicateur important de leur qualité et de leur comportement en combustion. La norme ISO 17225-4 définit plusieurs classes de teneur en cendres, allant de A0.5 (≤ 0,5% de cendres) à A10+ (> 10% de cendres). Les classes les plus courantes sont :
- A1.0 : ≤ 1,0% de cendres, qualité premium pour les petites installations
- A1.5 : ≤ 1,5% de cendres, standard pour la plupart des applications
- A3.0 : ≤ 3,0% de cendres, acceptable pour les grandes chaufferies
Une faible teneur en cendres réduit les besoins en maintenance et améliore l'efficacité de la combustion. Elle est particulièrement importante pour les petites installations où la gestion des cendres peut être problématique.
Applications et valorisation énergétique
Les plaquettes forestières trouvent de nombreuses applications dans le domaine de l'énergie, contribuant ainsi à la transition vers des sources renouvelables. Leur utilisation s'étend des petites chaudières domestiques aux grandes installations industrielles.
Chaufferies biomasse industrielles et collectives
Les chaufferies biomasse de moyenne et grande puissance constituent le principal débouché des plaquettes forestières. Ces installations, d'une puissance allant de quelques centaines de kilowatts à plusieurs mégawatts, alimentent des réseaux de chaleur urbains, des bâtiments publics, des industries ou des serres agricoles.
Les avantages des plaquettes pour ces applications sont nombreux :
- Un approvisionnement local et durable
- Une grande flexibilité d'utilisation
- Des coûts d'exploitation compétitifs par rapport aux énergies fossiles
- Une réduction significative des émissions de CO2
Les chaufferies modernes sont équipées de systèmes d'alimentation automatisés et de dispositifs de filtration des fumées, assurant un fonctionnement optimal et respectueux de l'environnement.
Cogénération dans les centrales à biomasse
La cogénération consiste à produire simultanément de l'électricité et de la chaleur à partir d'un même combustible. Les centrales de cogénération biomasse utilisent des plaquettes forestières pour alimenter une chaudière produisant de la vapeur à haute pression. Cette vapeur entraîne une turbine couplée à un alternateur pour générer de l'électricité, tandis que la chaleur résiduelle est valorisée pour le chauffage ou des procédés industriels.
Cette technologie présente plusieurs avantages :
- Une efficacité énergétique globale élevée (jusqu'à 80-90%)
- Une production d'électricité décentralisée et stable
- Une valorisation optimale de la ressource biomasse
Les centrales de cogénération biomasse jouent un rôle croissant dans le mix énergétique, contribuant à la stabilité du réseau électrique tout en fournissant une chaleur renouvelable.
Gazéification pour production de biogaz
La gazéification est un procédé
thermique de conversion de la biomasse en un gaz combustible appelé syngaz. Cette technologie offre de nouvelles perspectives pour la valorisation des plaquettes forestières, notamment pour la production de biocarburants avancés et de biogaz injectable dans les réseaux.Le processus de gazéification se déroule en plusieurs étapes :
- Séchage et pyrolyse du bois
- Oxydation partielle des produits de pyrolyse
- Réduction des gaz obtenus
Le syngaz produit, composé principalement de monoxyde de carbone, d'hydrogène et de méthane, peut être utilisé de différentes manières :
- Combustion directe pour la production de chaleur et d'électricité
- Méthanation pour la production de biométhane
- Synthèse de biocarburants liquides (procédé Fischer-Tropsch)
La gazéification présente plusieurs avantages par rapport à la combustion directe des plaquettes :
- Une meilleure efficacité énergétique globale
- Une plus grande flexibilité d'utilisation du gaz produit
- Des émissions polluantes réduites
Cependant, cette technologie reste encore peu mature à l'échelle industrielle et nécessite des investissements importants. Son développement pourrait ouvrir de nouvelles perspectives pour la valorisation des ressources forestières.
Enjeux économiques et environnementaux de la filière
Le développement de la filière des plaquettes forestières s'inscrit dans un contexte de transition énergétique et écologique. Il soulève des enjeux majeurs tant sur le plan économique qu'environnemental.
Gestion durable des ressources forestières
L'exploitation des plaquettes forestières doit s'intégrer dans une gestion durable des forêts. Cela implique de trouver un équilibre entre la production de bois-énergie et les autres fonctions de la forêt (production de bois d'œuvre, préservation de la biodiversité, stockage de carbone).
Plusieurs principes guident cette gestion durable :
- Respect des cycles de régénération naturelle des peuplements
- Maintien d'une partie des rémanents sur place pour préserver les sols
- Diversification des essences et des classes d'âge
- Protection des zones sensibles (zones humides, habitats d'espèces protégées)
La certification forestière (PEFC, FSC) joue un rôle important pour garantir ces pratiques durables. Elle permet aux consommateurs de s'assurer de l'origine responsable des plaquettes utilisées.
Bilan carbone et réduction des émissions de GES
L'utilisation des plaquettes forestières en substitution aux énergies fossiles permet de réduire significativement les émissions de gaz à effet de serre. Le bilan carbone de cette filière dépend cependant de plusieurs facteurs :
- La gestion durable de la ressource forestière
- Les distances de transport entre la forêt et le lieu d'utilisation
- L'efficacité des installations de combustion
Des études montrent que le bilan carbone des plaquettes forestières est généralement très favorable, avec des réductions d'émissions de l'ordre de 80 à 90% par rapport au gaz naturel ou au fioul. Ce bilan peut être encore amélioré en optimisant la logistique et en privilégiant les circuits courts.
Développement de l'économie locale et rurale
La filière des plaquettes forestières contribue au développement économique des territoires ruraux. Elle génère des emplois locaux non délocalisables, tout au long de la chaîne de valeur :
- Exploitation forestière et sylviculture
- Logistique et transport
- Installation et maintenance des chaufferies
On estime qu'un emploi est créé pour 2000 à 4000 tonnes de plaquettes forestières produites et consommées localement. Cette activité permet également de valoriser des ressources forestières qui n'avaient pas ou peu de débouchés auparavant, renforçant ainsi l'économie sylvicole.
Concurrence avec les autres usages du bois
Le développement de la filière plaquettes soulève la question de la concurrence avec les autres usages du bois, notamment le bois d'œuvre et l'industrie du panneau. Cette problématique, souvent résumée par l'expression "hiérarchie des usages", implique de trouver un équilibre entre les différentes valorisations de la ressource forestière.
Plusieurs pistes sont explorées pour limiter cette concurrence :
- Utilisation prioritaire des sous-produits et rémanents forestiers
- Développement de la sylviculture dynamique pour augmenter la production globale
- Amélioration du tri des bois pour optimiser leur valorisation
La mise en place de stratégies territoriales concertées, impliquant l'ensemble des acteurs de la filière bois, est essentielle pour assurer une gestion équilibrée de la ressource et pérenniser l'approvisionnement des différentes industries.